Demonstration
Dan demonstrated how to make Gnomes.
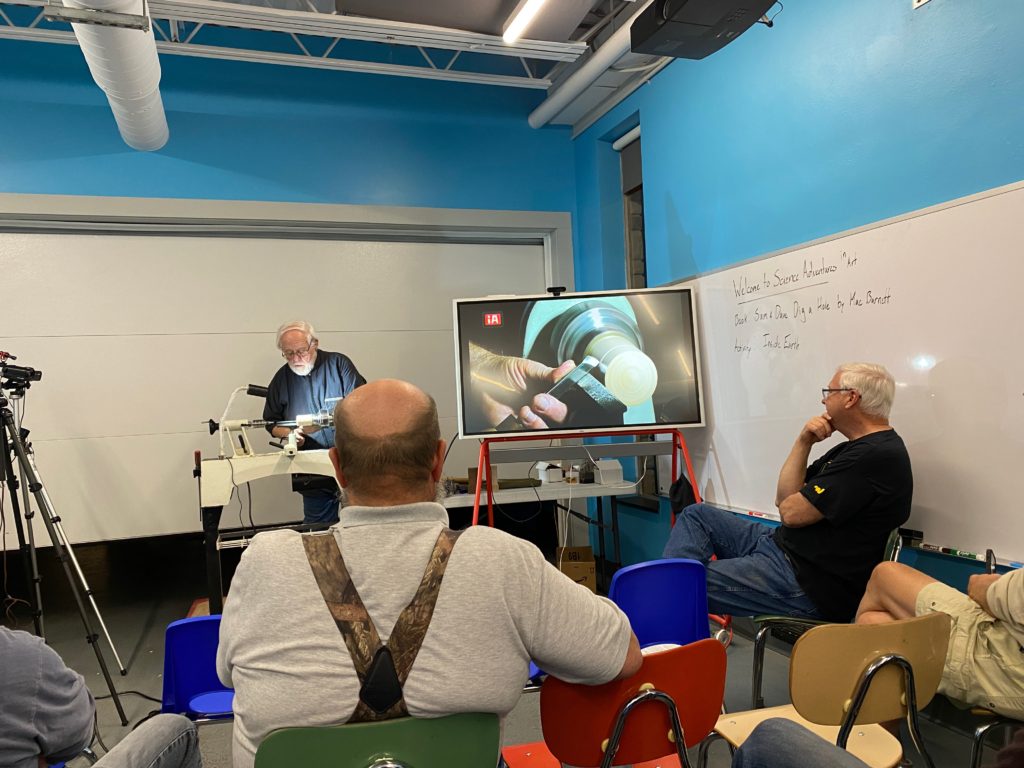

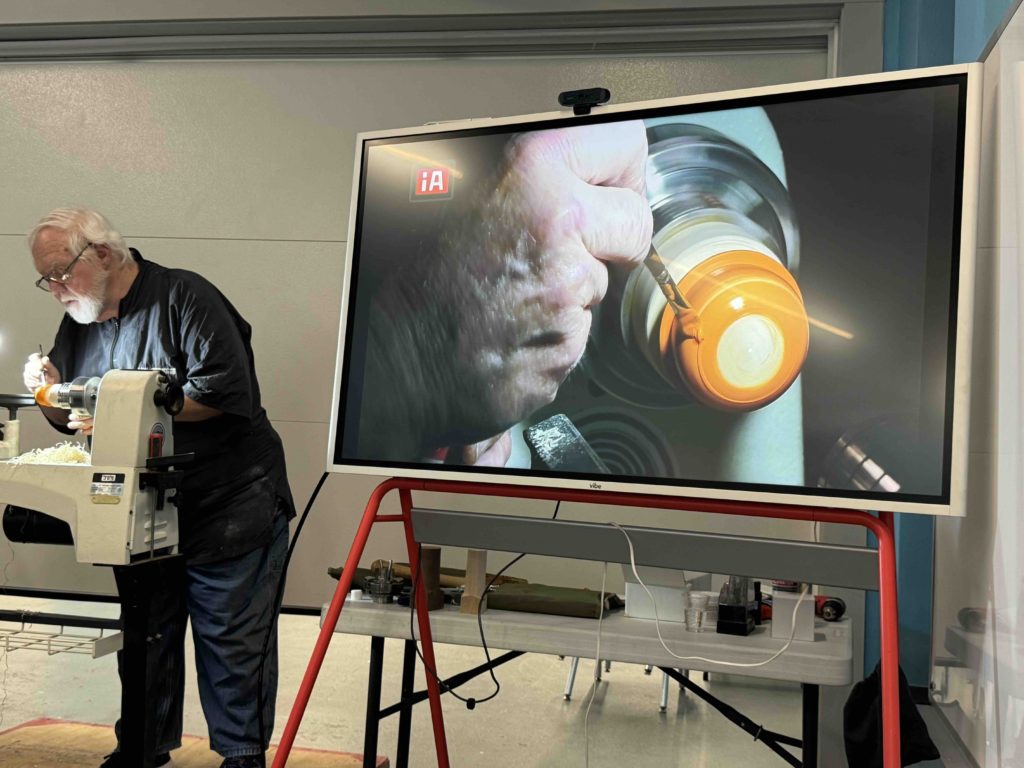
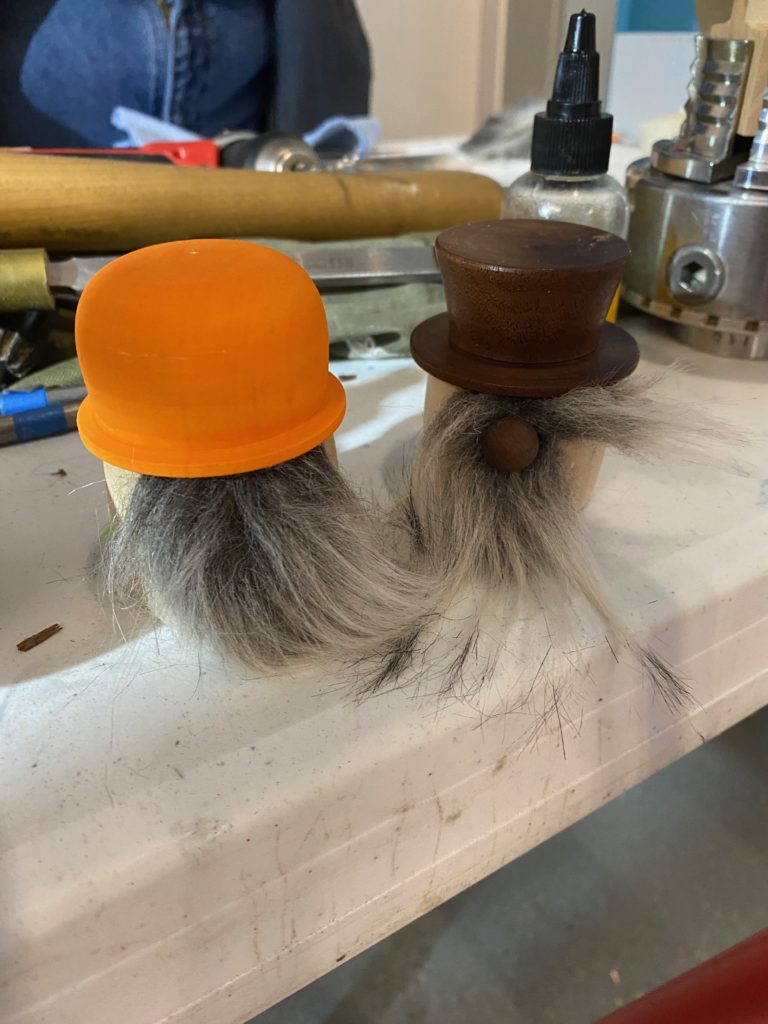
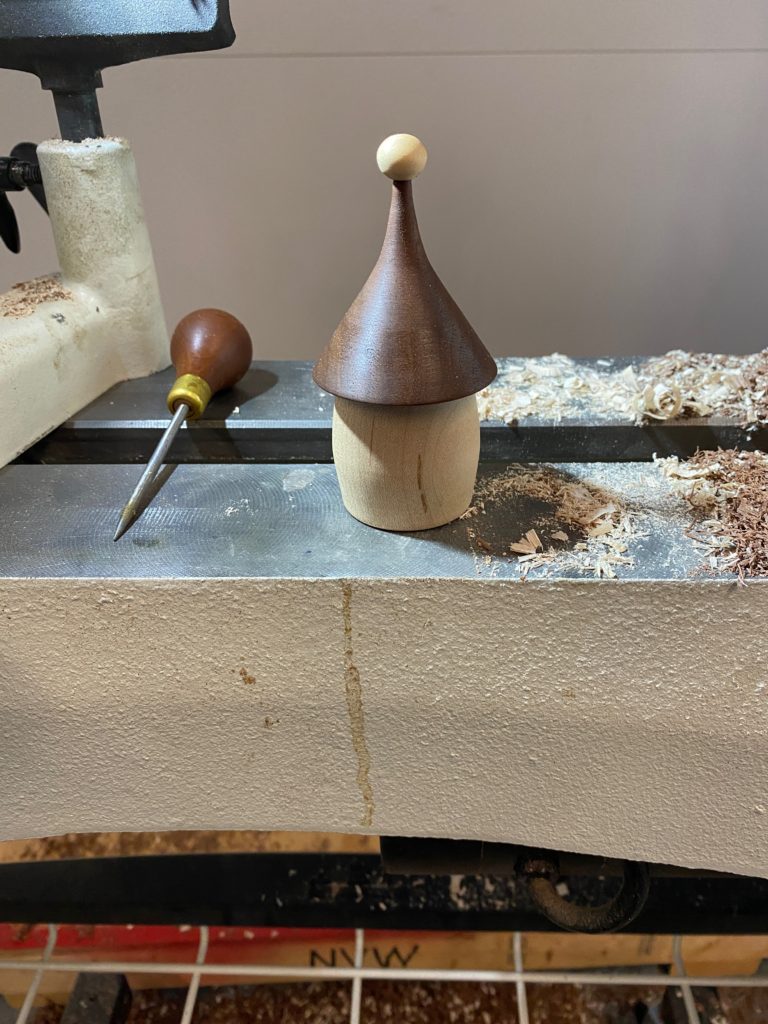
Dan provided notes so anyone can make a gnome like he does:
Show & Tell
We had a normal show and tell where we saw members amazing work
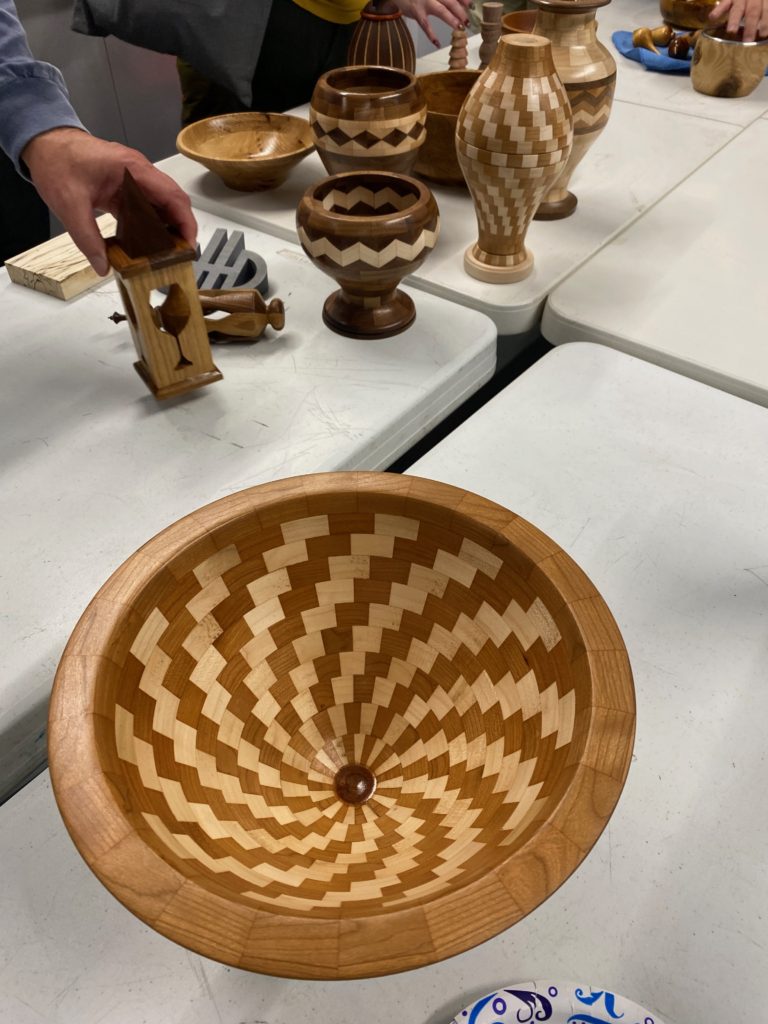
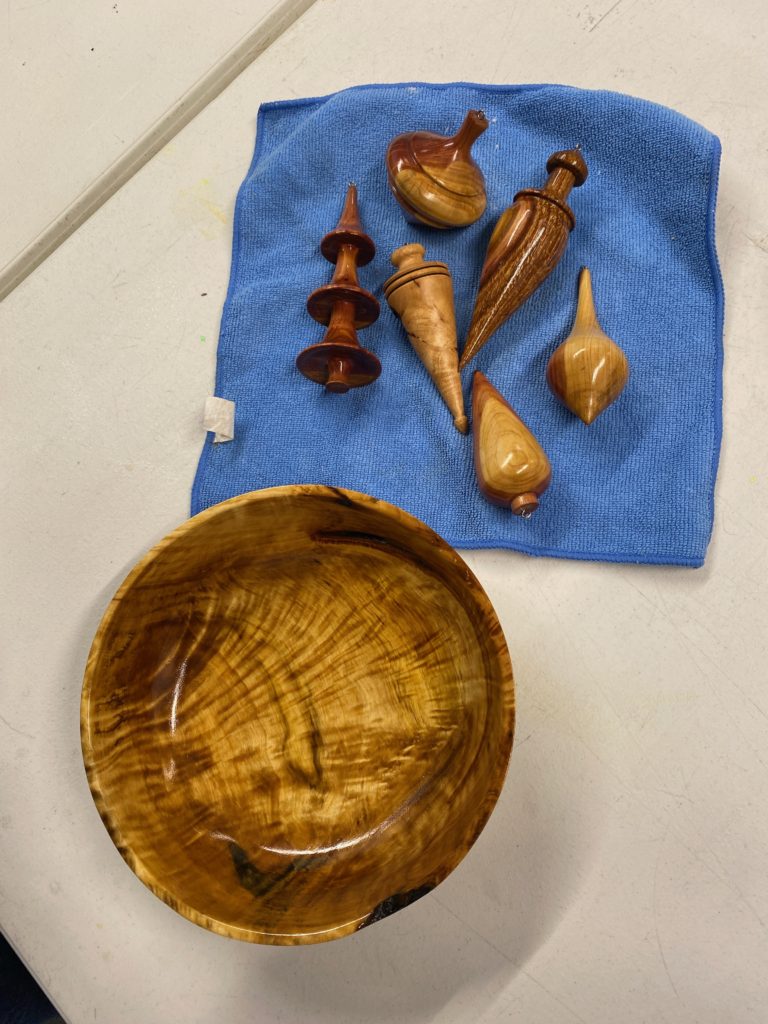
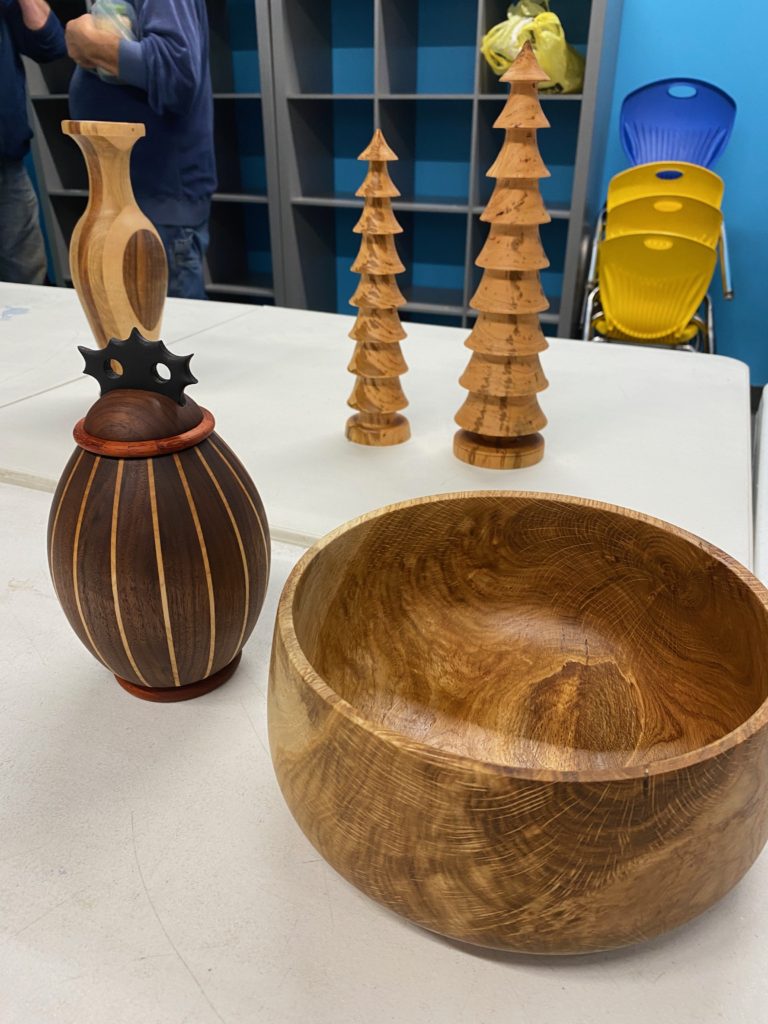
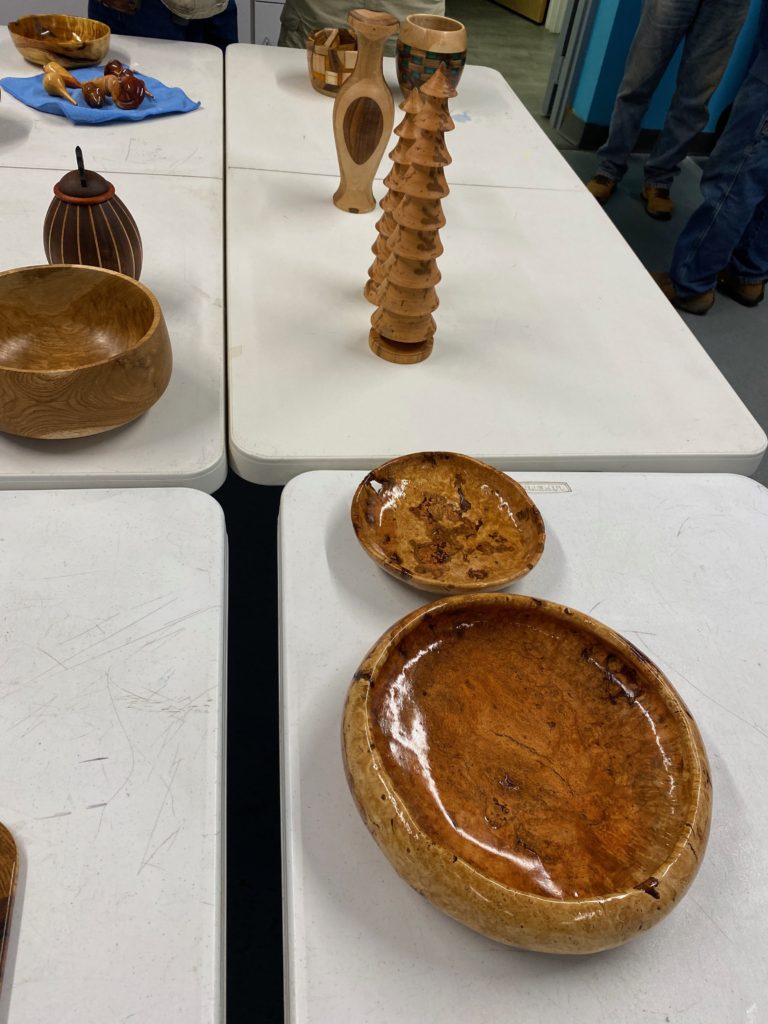
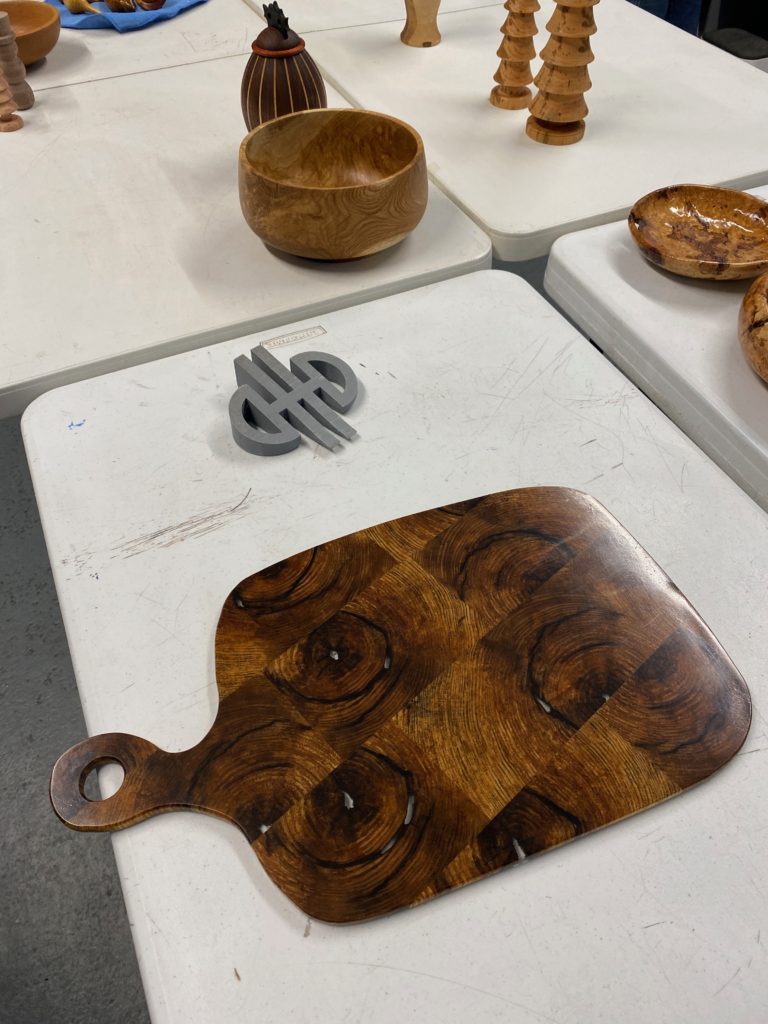
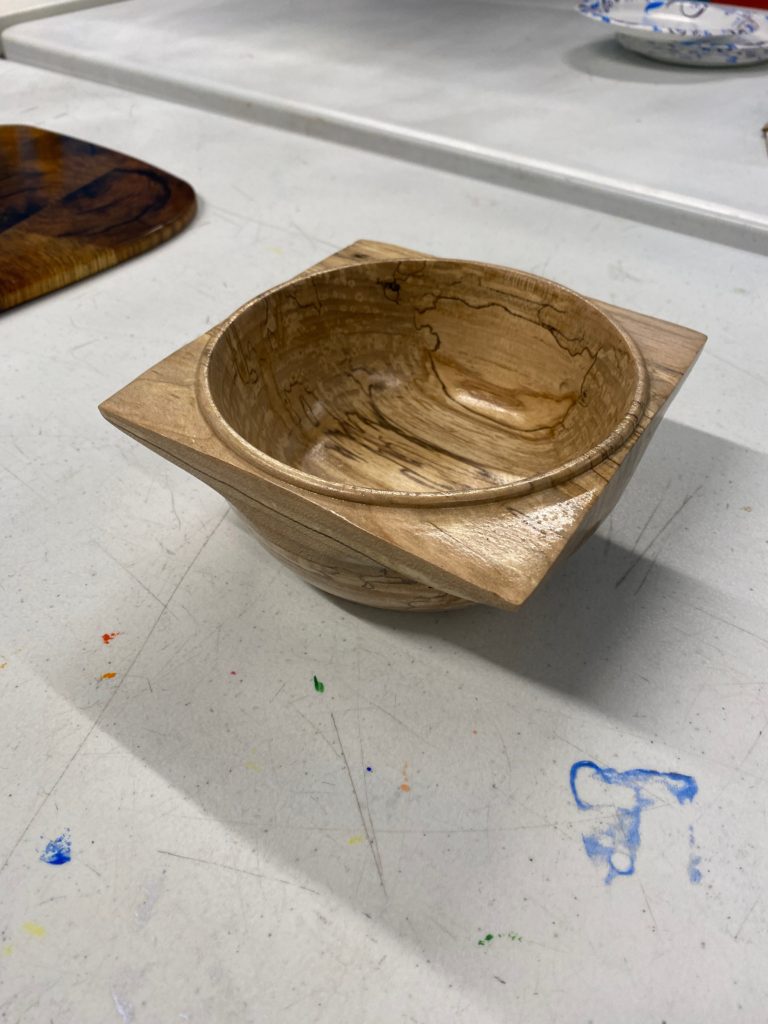
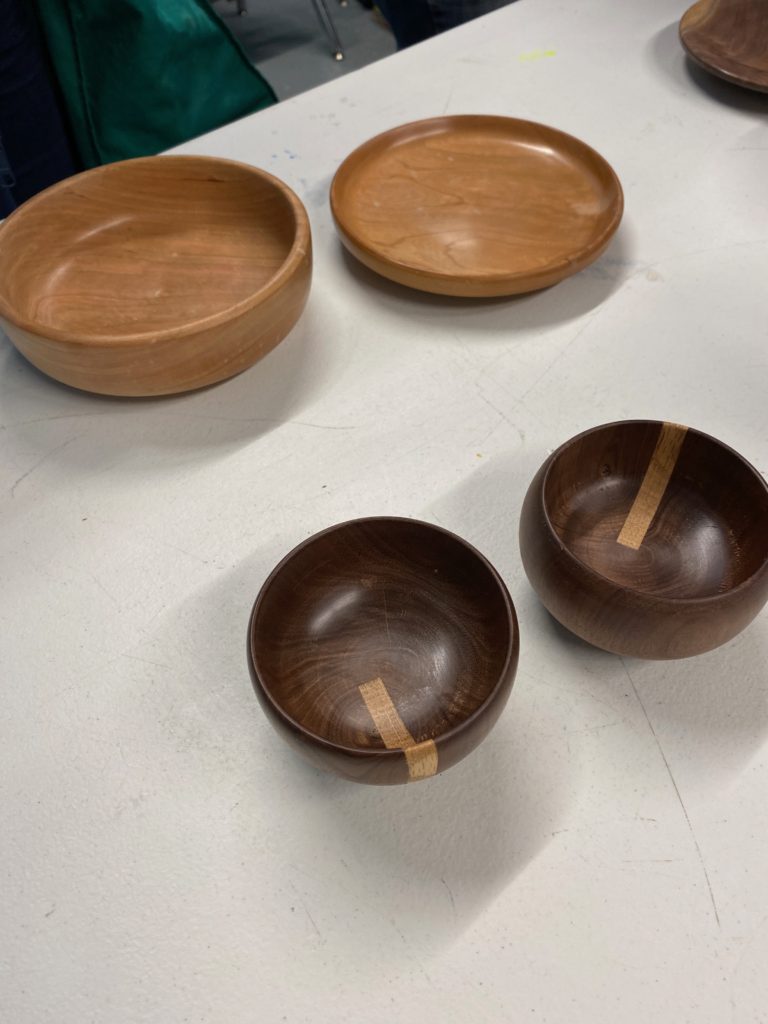
Demonstration
Dan demonstrated how to make Gnomes.
Dan provided notes so anyone can make a gnome like he does:
Show & Tell
We had a normal show and tell where we saw members amazing work
Paul Demmert shared how to make a Celtic Knot rolling pin. A Celtic knot is an infinite loop type pattern which makes an impressive decoration on a rolling pin. But first we had our regular show and tell where several people showed us what they’ve been making lately, from sculptures to grinders to chips and dip bowl.
Below are examples of various Celtic knots.
Below is an example of how to layout the cuts made in the blank before turning. You must make deep cuts just 1/8″ short of going through to hold it together until glued. Place a different colored 1/8″ thick wood blank in each slot, cut and glue one at a time.
Some other tips he shared:
Due to the demo lathe’s size limits Paul used smaller pieces to show how it’s done.
Look at this beautiful final product, when done on a full sized lathe.
Our first meeting after the summer break was a time to reconnect and learn what everyone made over the summer, so we had a larger than normal show and tell session as well as a great wood auction.
We had a normal meeting at the Rivet including a business discussions, show and tell and an in-depth presentation and sharpening demonstration by our very own Larry Lukens.
Several people showed the nice pieces they had created
Larry showed us how to sharpen our tools
We had a normal meeting in January which featured the business meeting, wood auction, show & tell as well as a discussion and walk through from Gib Corl on how he creates bowl blanks using left over hardwood flooring as well as how he recycles home wiring into a nice rim decoration.
The steps involved include:
This was our Holiday celebration meeting where everyone brought in something to eat and we had extra time to hang out and chat. We held a truncated business meeting, short wood auction and show & tell.
Paul Demmert discussed many different options of things you can make from skills gained after making pens. There are many things like coffee scoops, ice cream scoops, pizza cutters, measuring cups and spoons, and seam rippers which go together much like pens by tuning handles. You can find kits for such projects at places like Penn State Industries.
Some tips Paul shared from the classes he’s taught included:
Dan Kozar demonstrated how to make a mini wizard wand ornament and a freeform finial style ornament highlighting his skills with a skew.
Some of the tips he shared included:
It was a show & tell bonanza…everyone brought things they made since the May meeting, so there was a lot to share. So many amazing pieces from the talented turners in our club.
Paul Demmert walked through the various ways to attach and secure a wood blank to the lathe to make a bowl using a chuck, faceplate and even the drive spur.
We also had a great turnout for the show & tell at our meeting. Look at all the amazing work our members made recently.
Unfortunately we could not meet in March as planned due to a COVID outbreak at our normal meeting place, but our members had kept busy turning and below are some of the items we likely would have seen at the show & tell time. Enjoy the craftsmanship and hopefully it sparks some new ideas for you as well.
Stephen Tuttle not only sent a picture of what he’s been working on, he also explained how it was done, the plan and tools he used and how to get your own. We nearly got a virtual demonstration for this one.
Segmented Ornamental Carafe – Walnut, maple, padauk, 7 1/2″ x 14″h
After seeing a lot of fantastic work in the “segmented turning” realm I was inspired to try it myself.
These turnings have to start with a plan. You could do it on graph paper but I use inexpensive MAC software called iDraw.
Once you know the circumference of your piece this online segment calculator is very helpful to figure out the size of each segment.
http://www.woodturnersresource.com/extras/projects/segmentcalc/index.html
This jig greatly simplifies cutting accurate segments that make up each ring.
I made the “wedgie sled” following this YouTube video:
And I purchased “wedgies”, computer generated shapes for any angle or number of segments/ring, to set up the jig.
https://www.etsy.com/listing/850428444/segmented-bowl-wedgies-wedges-for
These two items worked very well to create tight joints in the rings. Rings are glued up using hose clamps that can be gotten at any hardware store.
Once all the rings are made they are glued in a stack. I did this incrementally – the bottom half of bowl section was done first and notched to receive top half. The throat was a little different as the sections are staves and not cut with the sled. This was turned separately and glued to the completed bowl section.
This technique is definitely not for everyone as it is more figurin’, calculatin’, cuttin’ and gluin’ than turning. If I do more of it I think I will keep it simple. I don’t think a 10,000 piece masterwork you see online is in my future. It does have positives in that it can be done with many of the scraps that accumulate in a shop. There are no drying issues. There isn’t any end grain exposed in the circumference of the turning. You can make a large bowl with more manageable pieces of wood.
I know I have seen this shape before, but where?…
Perhaps our next president’s challenge should be making Genie bottles. Now you have all you need to make your own.