Demonstration
Dan demonstrated how to make Gnomes.
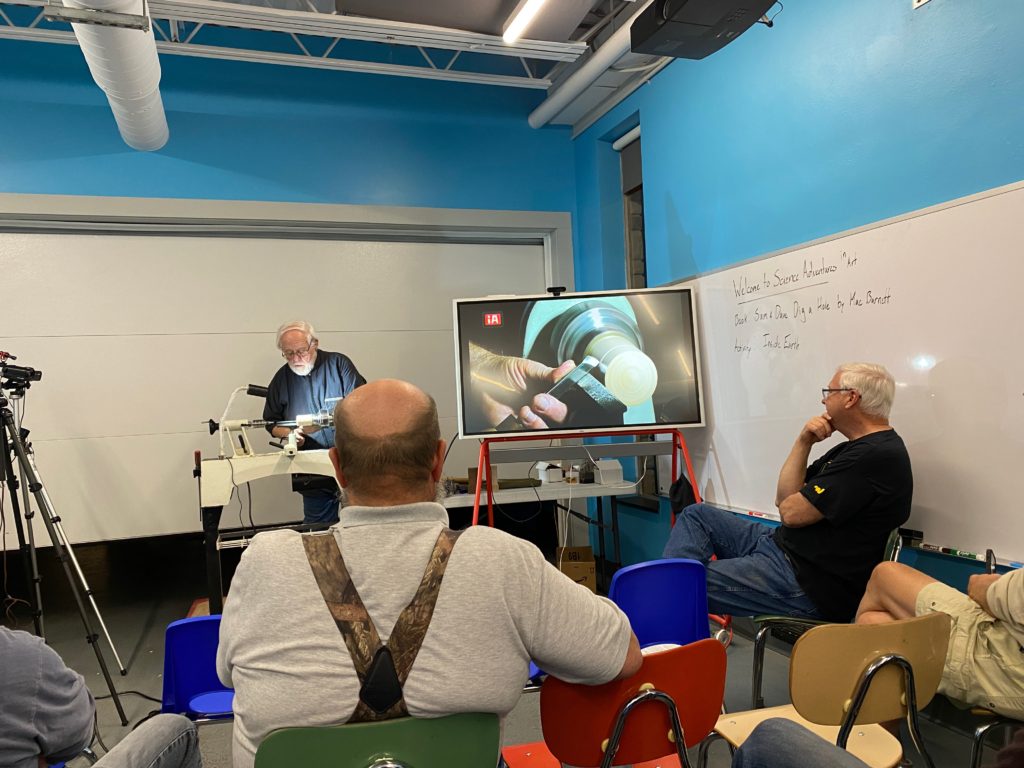

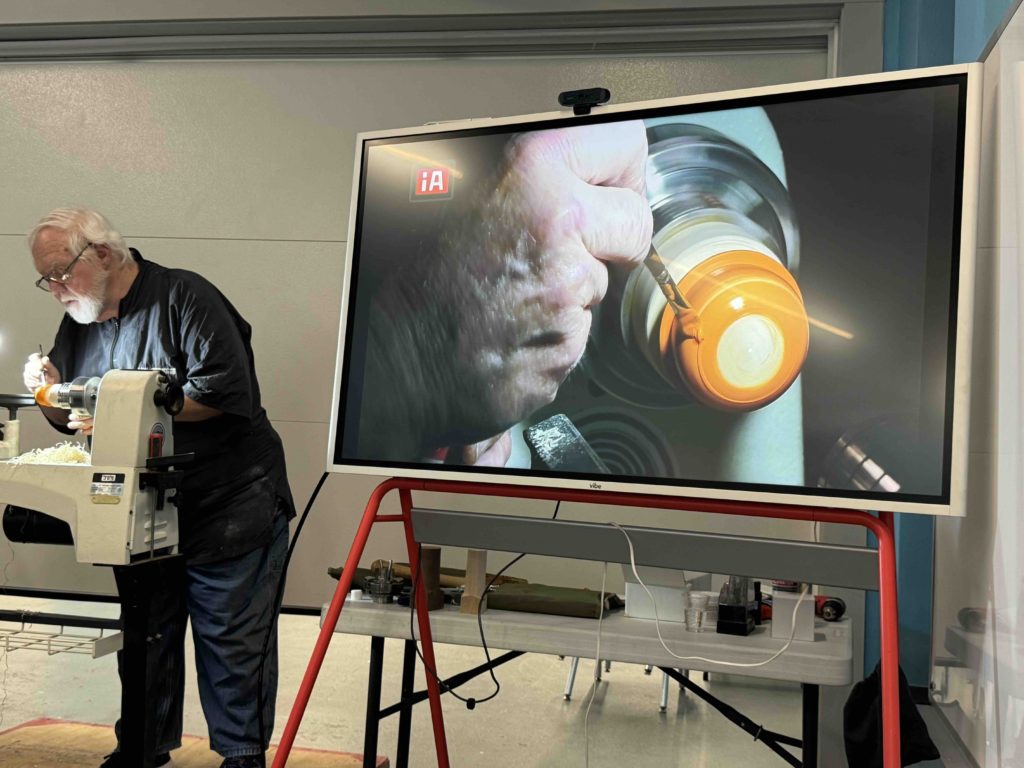
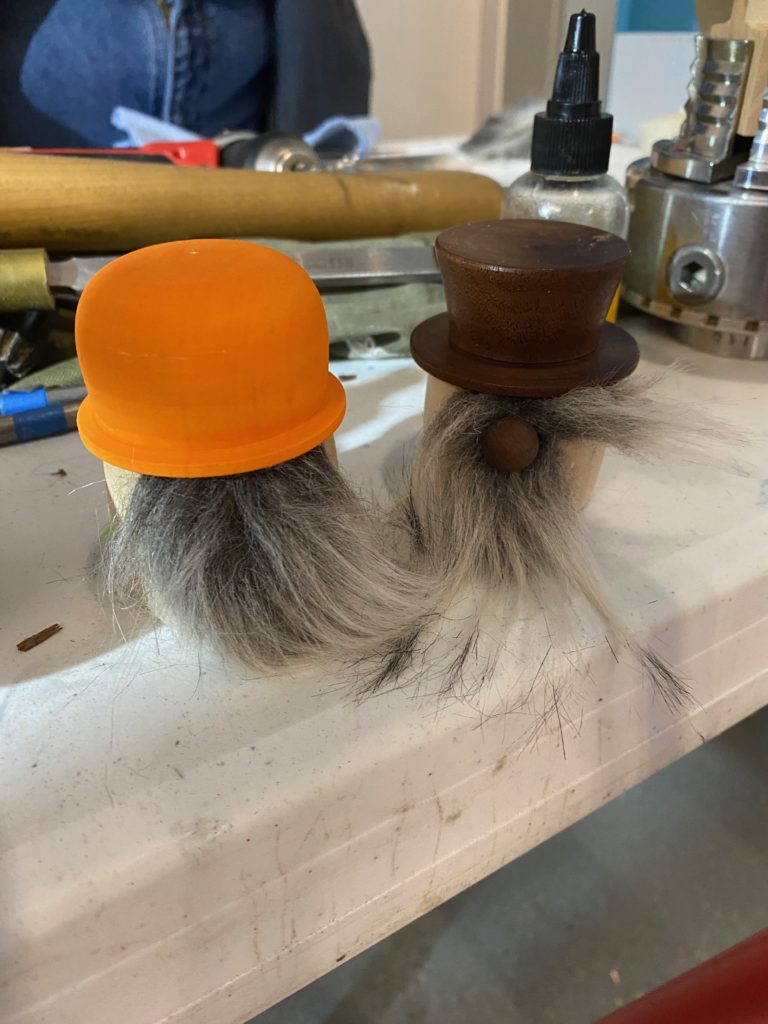
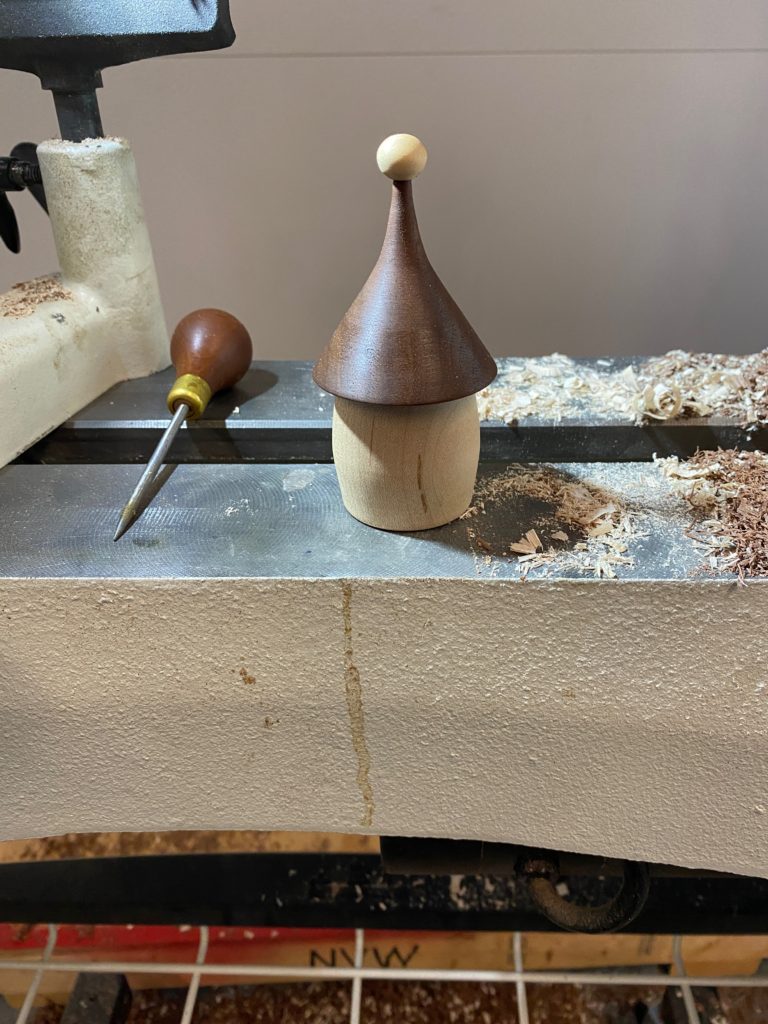
Dan provided notes so anyone can make a gnome like he does:
Show & Tell
We had a normal show and tell where we saw members amazing work
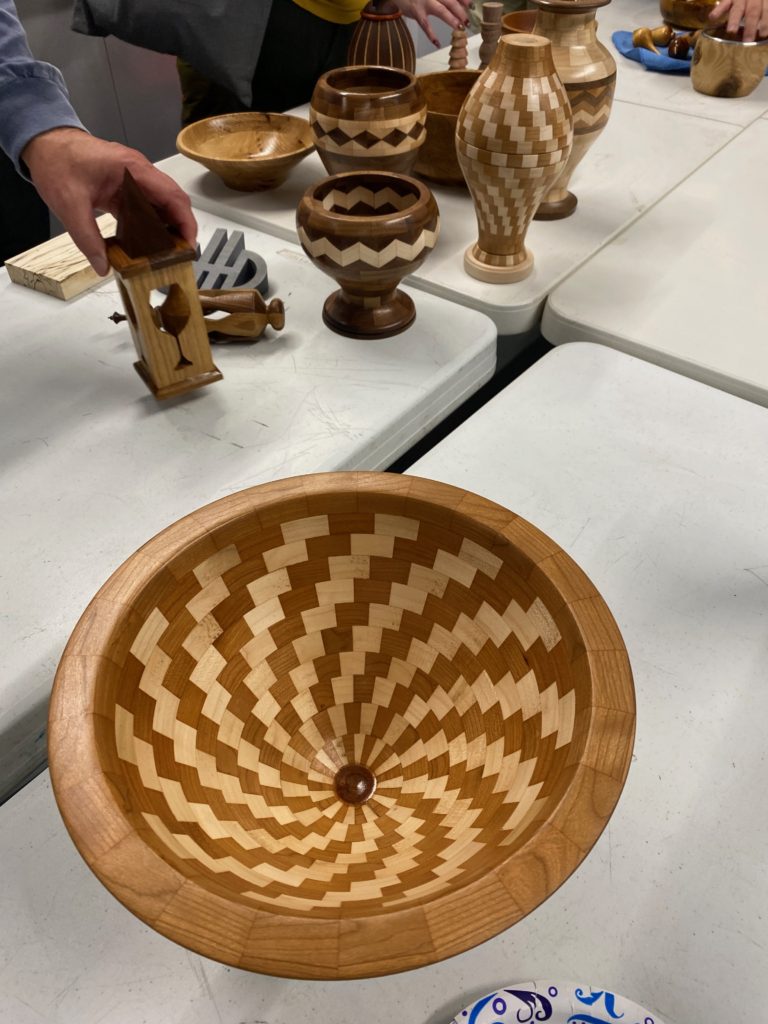
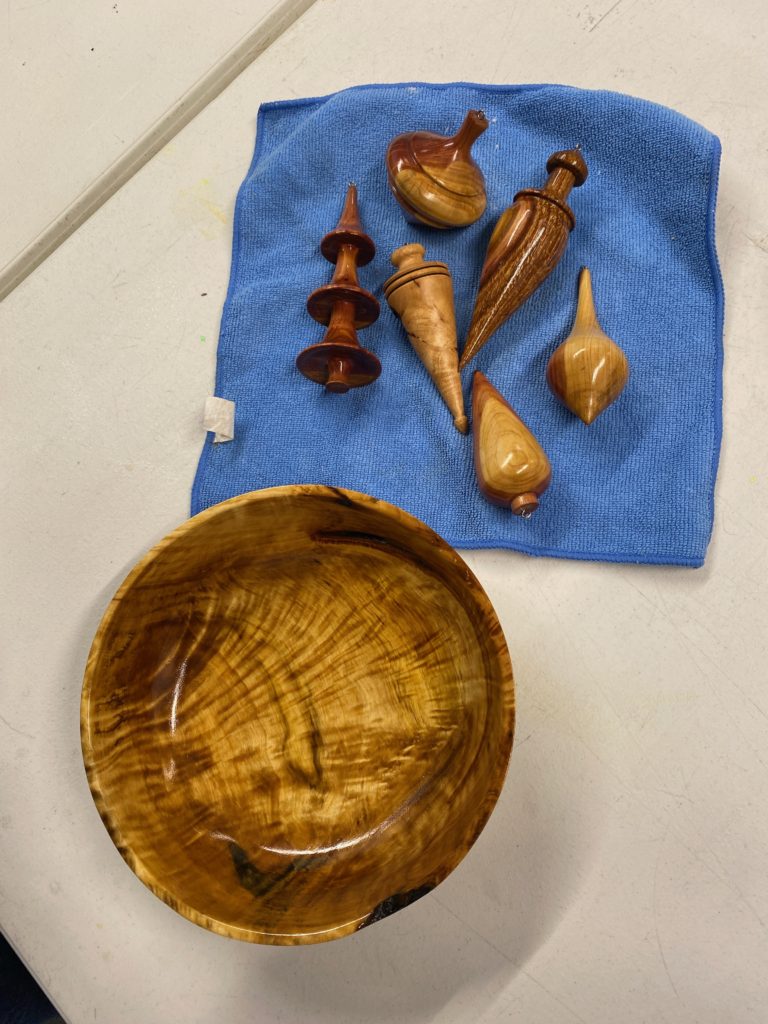
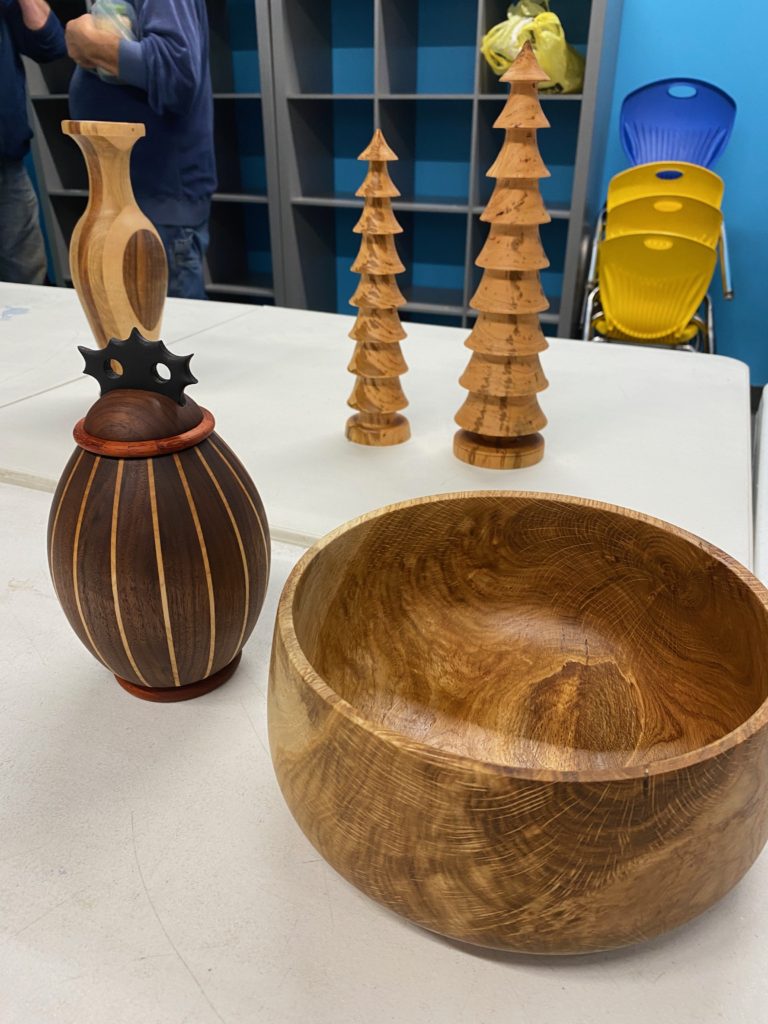
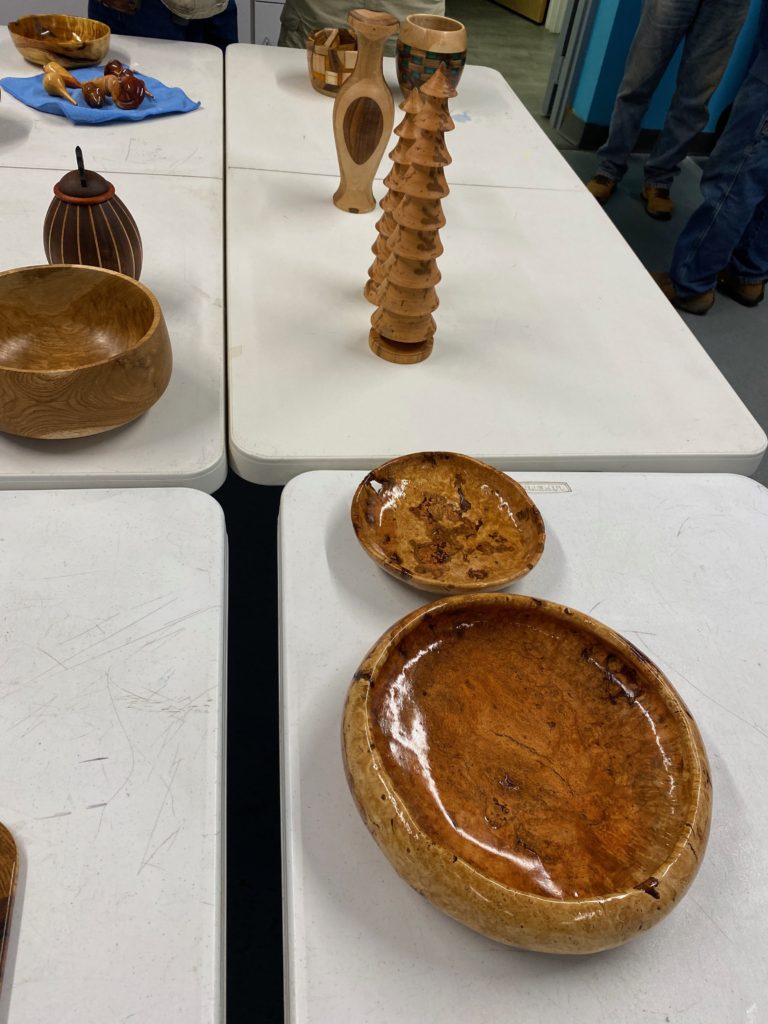
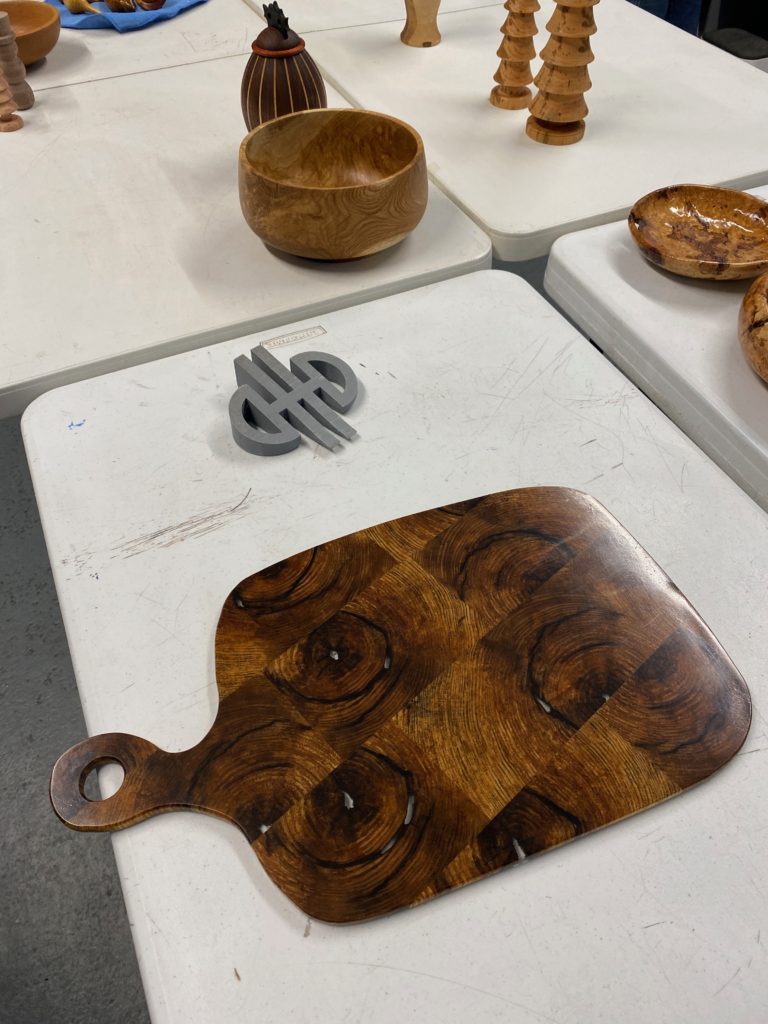
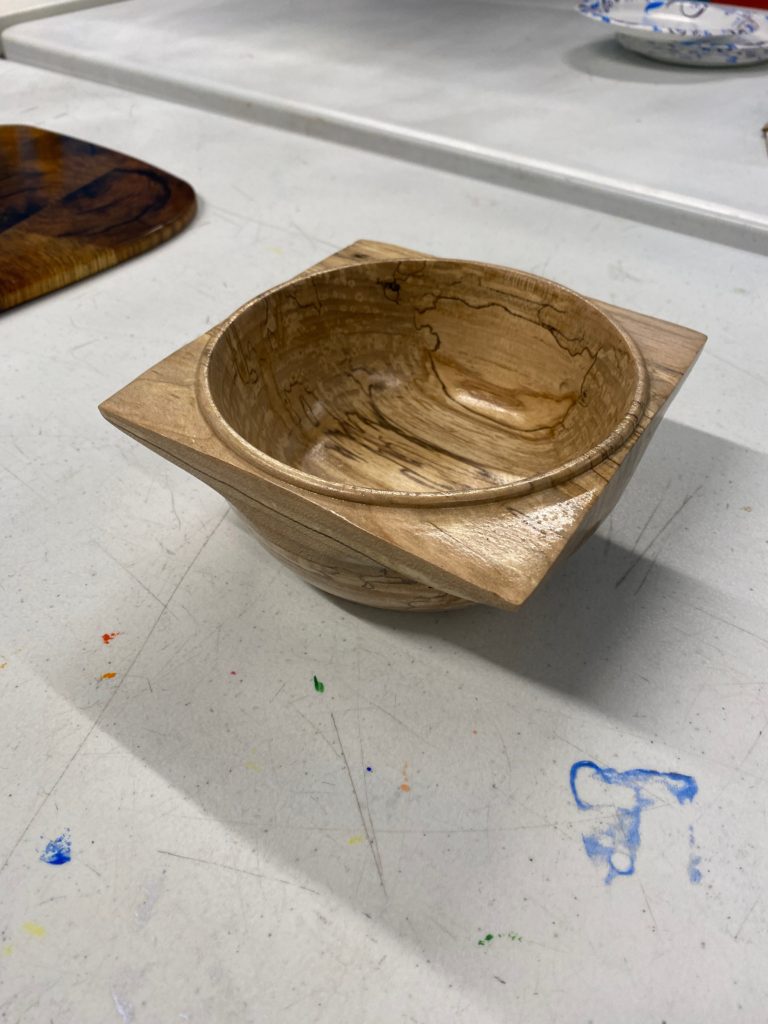
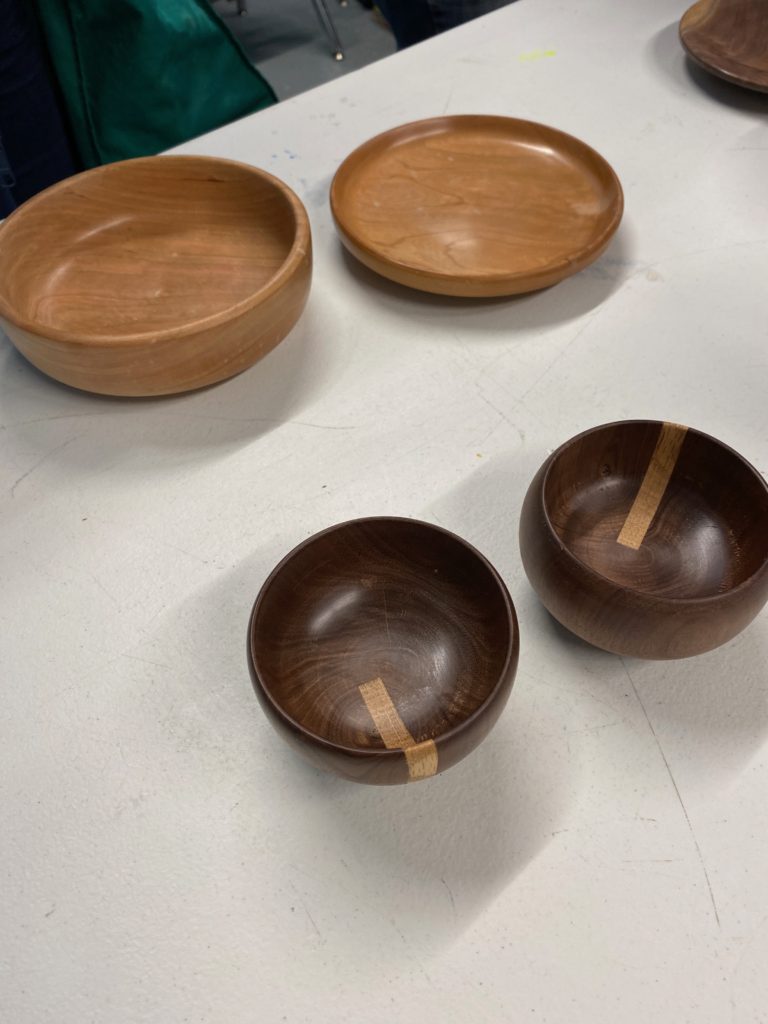
Demonstration
Dan demonstrated how to make Gnomes.
Dan provided notes so anyone can make a gnome like he does:
Show & Tell
We had a normal show and tell where we saw members amazing work
Paul Demmert shared how to make a Celtic Knot rolling pin. A Celtic knot is an infinite loop type pattern which makes an impressive decoration on a rolling pin. But first we had our regular show and tell where several people showed us what they’ve been making lately, from sculptures to grinders to chips and dip bowl.
Below are examples of various Celtic knots.
Below is an example of how to layout the cuts made in the blank before turning. You must make deep cuts just 1/8″ short of going through to hold it together until glued. Place a different colored 1/8″ thick wood blank in each slot, cut and glue one at a time.
Some other tips he shared:
Due to the demo lathe’s size limits Paul used smaller pieces to show how it’s done.
Look at this beautiful final product, when done on a full sized lathe.
We had a normal meeting at the Rivet including a business discussions, show and tell and an in-depth presentation and sharpening demonstration by our very own Larry Lukens.
Several people showed the nice pieces they had created
Larry showed us how to sharpen our tools
This was our Holiday celebration meeting where everyone brought in something to eat and we had extra time to hang out and chat. We held a truncated business meeting, short wood auction and show & tell.
Paul Demmert discussed many different options of things you can make from skills gained after making pens. There are many things like coffee scoops, ice cream scoops, pizza cutters, measuring cups and spoons, and seam rippers which go together much like pens by tuning handles. You can find kits for such projects at places like Penn State Industries.
Some tips Paul shared from the classes he’s taught included:
Dan Kozar demonstrated how to make a mini wizard wand ornament and a freeform finial style ornament highlighting his skills with a skew.
Some of the tips he shared included:
This month’s meeting featured an interactive remote demonstration (IRD) by Don Wilson showing us how to turn a sphere, with the tricks he’s learned from making hundreds over his many years turning.
We enjoyed some holiday treats prior to our show and tell where we shared the first thing we turned. Some of us started turning months ago, others brought decades old pieces. It was fun to hear how we all started out. Ken Vasko also demonstrated how he makes several different Christmas ornaments and decorations.
The Reeds Gap Fall Festival, Saturday Oct 8th, was a great success. We had a lot of interest in woodturning and our club. There was about 1200 people at the event. It was a lot of fun and we met a lot of good people.
Special thanks to Travis Gross, Brian Hummel and S. Bear for helping setup, turn, schmooze the crowd, tear down and clean up!
New club member is a great demonstrator. He drew a crowd for sure.
The demonstration for this meeting was be provided by Ken Vasko. It was a really good follow-up to the presentation at the December meeting about Easy Wood Tools.
Ken covered:
Our previously scheduled presenter had to cancel for personal reasons this month so our pivot was to watch a video about befriending the skew by Alan Lacer. If you have any reservations about using the skew, join us as we watch Alan break it down, show how to sharpen it, use it for 8 different cuts and discover why it can grab and how to avoid catches.